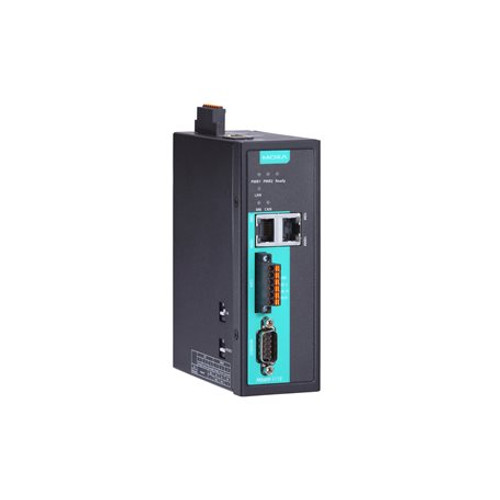
MOXA MGate 5118-T
MGate 5118 SeriesDatasheet
Features and Benefits
- Converts J1939 to Modbus, PROFINET, or EtherNet/IP
- Supports Modbus RTU/ASCII/TCP master/client and slave/server
- Supports EtherNet/IP Adapter
- Supports PROFINET IO device
- Supports J1939 protocol
- Effortless configuration via web-based wizard
- Built-in Ethernet cascading for easy wiring
- Embedded traffic monitoring/diagnostic information for easy troubleshooting
- microSD card for configuration backup/duplication and event logs
- Status monitoring and fault protection for easy maintenance
- CAN bus and serial port with 2 kV isolation protection
- -40 to 75°C wide operating temperature models available
- Security features based on IEC 62443
Introduction
The MGate 5118 industrial protocol gateways supportthe SAE J1939 protocol, which is based on CAN bus (Controller AreaNetwork). SAE J1939 is used to implement communication and diagnosticsamong vehicle components, diesel engine generators, and compressionengines, and is suitable for the heavy-duty truck industry and backuppower systems. It is now common to use an engine control unit (ECU)to control these kinds of devices, and more and more applicationsare using PLCs for process automation to monitor the status of J1939devices connected behind the ECU.
The MGate 5118 gateways support the conversionof J1939 data to Modbus RTU/ASCII/TCP, EtherNet/IP, or PROFINET protocolsto support most PLC applications. Devices that support the J1939 protocolcan be monitored and controlled by PLCs and SCADA systems that usethe Modbus RTU/ASCII/TCP, EtherNet/IP, and PROFINET protocols. Withthe MGate 5118, you can use the same gateway in a variety of PLC environments.
Key-in-Free J1939 Command
The J1939 protocol is designed to retrieve a wide range of data from CAN-J1939 devices. To eliminate the need to key in all J1939 commands into the gateway by hand, MGate 5118 gateways can auto detect the output commands used by the CAN device.
With a single click in the web console, all of the output commands from your CAN device will be detected by the gateway automatically. The commands will be displayed in the web console’s command list, and then can be further modified by the user if needed. The MGate 5118 gateways make it much easier for users to connect PLCs with CAN devices.
A Variety of Maintenance Functions
The MGate 5118 gateways support a web console for easy configuration and maintenance, and the built-in traffic monitor function monitors J1939 protocol traffic, allowing users to monitor the status of connected CAN devices, including error count, packet count, and bus-offline. The traffic monitor function can also be used to troubleshoot CAN devices. The diagnostics tool helps users to check CAN device settings and indicates CAN device availability by reading the J1939 network address. In addition, the MGate 5118 gateways have a built-in Live List function for when two or more J1939 devices are connected to the same CAN bus. This function shows the PGN and address of packets transmitted from each device, giving users the ability to gage the loading of the CAN bus.
To detect loose cables, the MGate 5118 gateways support status monitoring and fault protection functions. The status monitoring function notifies a PLC when the cable between the gateway and CAN device is loose. In addition, the fault protection function executes actions predefined by the user when the cable between the gateway and PLC is loose.